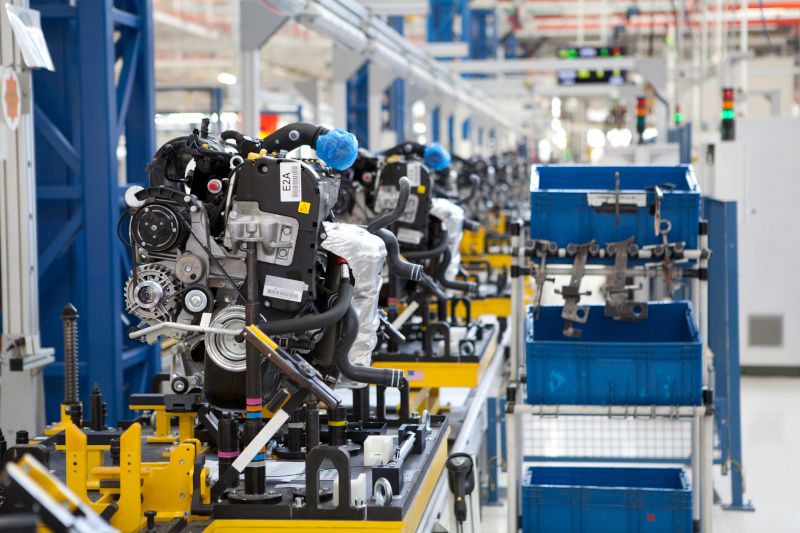
LEAN Consulting
For many companies, the term LEAN represents nothing more than an outdated management tool from the 2000s. For most people, however, the lean factory concepts are the basis of their operational success today - and that's how we see it too. Even in the age of digitalization and artificial intelligence. With more than 30 years of experience in LEAN consulting, we support HANDS-ON companies on their way to becoming world-class in production (Lean Manufacturing) or in the indirect area (LEAN Office).

Interested in the topic of LEAN? Industry and implementation examples? Just contact me, I'll be happy to help by phone or email.
Walter Meitz
+43 664 654 06 79
This email address is stez protected from spambots. You need javaScript Enabled to view it.
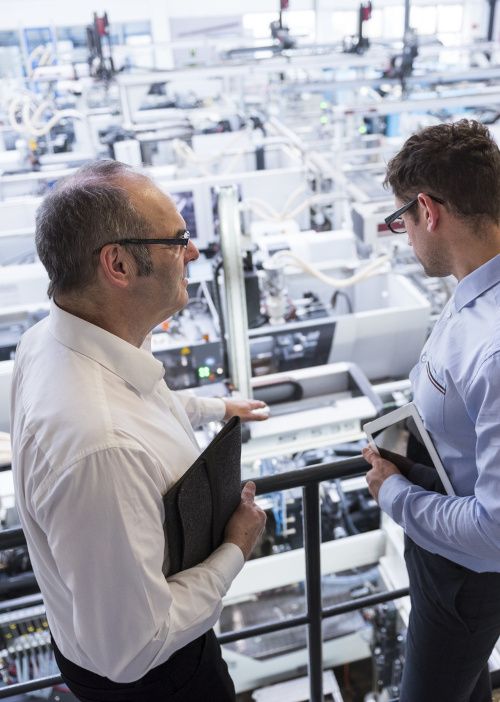
Implementation-oriented LEAN consulting
Implementation-oriented consulting represents an essential approach to supporting companies and organizations in the successful implementation of changes, projects and strategic goals. This form of consulting does not only focus on theoretical concepts, but also puts the emphasis on the practical implementation of projects. Implementation-oriented consulting is characterized by the fact that it goes beyond the mere development of ideas and strategies. Your main goal is to accompany the practical implementation of changes and to ensure that the planned measures are successfully implemented. This approach requires close collaboration between consultants and employees at all levels of an organization.
Advantages of implementation orientation
- Practical solutions: Instead of abstract theories, concrete solutions are developed that meet the specific needs and challenges of a company.
- Faster results: Focusing on implementation leads to faster results and ensures that changes are implemented more efficiently.
- Employee engagement: Involving employees in the implementation process creates a higher level of commitment and a stronger identification with the changes.
- Measurable success: Implementation-oriented consulting places emphasis on measurable results and success monitoring, which enables continuous improvement.
- Sustainability: The solutions developed are often more sustainable because employees actively shape and adopt them.
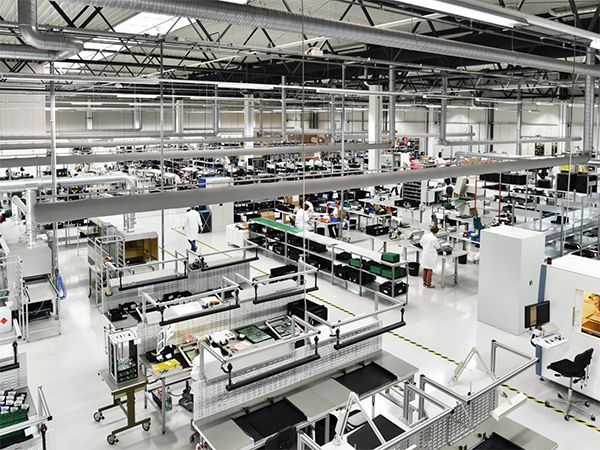
LEAN PRODUCTION
In today's economic world, where efficiency and competitiveness are of central importance, the consistent implementation of the LEAN production philosophy has established itself as an indispensable approach for companies operating at a world-class level.
LEAN Production is a powerful approach that helps companies optimize their production processes, reduce waste and achieve sustainable increases in efficiency. By applying LEAN principles, companies can not only reduce costs, but also strengthen their competitiveness and ensure higher product quality. In a constantly changing business world, LEAN Production is a proven way to act in a future-oriented and successful manner.
Lean production consulting and training from a single source
In an increasingly competitive economy, optimizing production processes is essential. Our consulting services in the area of lean production support companies in reducing waste, streamlining processes and creating more sustainable value. But we go one step further: In addition to strategic advice, we offer a comprehensive training program that enables your employees to effectively implement the principles of lean production.
Consulting: Tailor-made lean strategies for your company
Our approach begins with a precise analysis of your existing processes. Together we identify optimization potential and develop an individual roadmap that is based on the specific requirements of your company. Whether introducing Kanban, just-in-time principles or implementing 5S – we accompany you from conception to implementation.
Training: Lean competence at all levels
Sustainable success occurs when all employees internalize the lean philosophy. We therefore offer practice-oriented training for different target groups – from shop floor employees to management levels. Our trainings include:
- Basics of Lean Production: Introduction to the principles and tools
- Kaizen workshops: making continuous improvement tangible
- Value Stream Mapping: Optimizing the value chain
- Management training: Lean leadership for sustainable cultural change
Your added value
By combining consulting and training, you not only receive optimized processes, but also a team that continuously develops them. Our expertise is based on more than 200 successfully implemented projects – from medium-sized companies to global corporations.
Rely on efficiency and expertise. Contact us today to start your lean production strategy together with us.
LEAN principles
Value orientation is the foundation of lean production and puts the customer at the center of all company activities. The concept begins with the fundamental question: What exactly does the customer value about the product or service? In this context, “value” is understood as something that the customer is willing to pay because it meets their needs or solves their problems. Companies need to delve deeply into the customer perspective to accurately understand these needs and define which aspects of the product or service actually add value.
A company that takes value orientation seriously ensures that every step in the production process is aimed directly at creating that value. This includes minimizing or completely eliminating non-value-adding activities that offer no direct benefit to the customer. These activities are often viewed as waste and can be grouped into categories such as overproduction, waiting times, unnecessary transportation, excess inventory, excessive processing, unnecessary movements, and errors. By focusing strictly on creating value, companies can use their resources more effectively, increase customer satisfaction and ultimately increase their competitiveness.
Value stream analysis is a strategic tool in lean production that helps companies examine the entire production process and understand how value flows - from the receipt of raw materials to the delivery of the final product to the customer. The aim of this analysis is to map and evaluate each individual step in the process in order to make the actual value streams and also the inefficiencies that occur visible.
This process typically begins with the creation of a value stream map that maps all activities in the production process, both value-adding and non-value-adding. By visually representing the value stream, companies can easily identify bottlenecks, unnecessary wait times, redundant work steps and other forms of waste. On this basis, they can then take targeted measures to increase efficiency, shorten throughput times and improve the flow of production. Value stream analysis is not only a tool for identifying problems, but also an essential step in planning and implementing strategic improvements and optimizations throughout the entire production process.
The flow principle is a central pillar of lean production and strives to design the production process so that materials and information flow continuously and without interruptions through the value chain. This principle is based on the knowledge that interruptions in the production flow - whether due to bottlenecks, waiting times or inefficient work processes - can lead to significant waste and reduce the overall efficiency of production.
An optimized flow means that each production step flows seamlessly into the next, without the need for intermediate storage of materials or unused resources. This requires careful planning and synchronization of production processes to ensure that all resources - machines, materials, labor - are always available and used optimally. A continuous flow reduces production time and minimizes costs by requiring fewer resources to manage inventory and waiting times. In addition, a fluid production process helps increase the company's flexibility, allowing it to respond more quickly to changes in demand.
The pull principle is another central concept in lean production, which aims to strictly align production and warehousing with actual demand. Instead of producing products in large quantities in stock on suspicion and based on forecasts (as is the case with the push principle), with the pull principle products are only manufactured when there is concrete demand. This ensures that only what the customer really needs is produced, thus preventing overproduction and the associated high storage costs.
The pull principle requires close coordination and communication along the entire supply chain to ensure that the necessary materials and components are available exactly when they are needed. This not only reduces inventory requirements, but also the risk of being left with unsold products that may become obsolete or no longer meet current customer needs. In addition, the pull principle enables greater flexibility and responsiveness, as companies are able to quickly adapt their production to changes in demand without risking high upfront costs. It promotes more efficient use of resources and supports just-in-time production, where materials and parts are provided at exactly the right time to support the production process.
Continuous improvement, known as Kaizen, is at the heart of lean production and embodies a philosophy based on constant, incremental improvement. Kaizen is more than just a process; it is an attitude and a corporate culture that aims to optimize every aspect of production and business operations. This approach emphasizes that it is not necessarily the big, radical changes that make the biggest difference, but rather the sum of many small improvements implemented continuously and consistently over time.
Kaizen encourages every employee in the company, regardless of their position, to actively look for ways to improve workflows, processes, quality and efficiency. Involving all employees in the improvement process not only increases productivity, but also promotes the motivation and commitment of the workforce. This collective effort results in a dynamic, learning organization that can respond flexibly to change and continually grow. Kaizen also promotes an open communication culture in which suggestions and ideas from all levels of the company are welcomed and actively encouraged. Ultimately, this philosophy leads to constant development of the company, which enables it to remain competitive in the long term and to react proactively to market changes.
Advantages of using LEAN management
Lean principles help companies to streamline their processes and eliminate waste in all forms. The consistent focus on value-adding activities significantly increases efficiency. Resources such as time, materials and manpower are used specifically and effectively. This not only leads to higher productivity, but also to better utilization of existing capacities.
The focus on continuous improvement (Kaizen) leads to constant optimization of products and processes. Errors and defects are identified early and corrected before they cause major problems. By involving all employees in the improvement process, a high quality culture is created, which is reflected in the reliability and longevity of the products.
Lean principles contribute significantly to reducing operating costs. By avoiding overproduction, minimizing inventory, and using resources efficiently, companies can significantly reduce costs. At the same time, just-in-time production enables needs-based procurement, which brings additional savings.
In a constantly changing market environment, the ability to adapt quickly is crucial. Lean methods promote a flexible production method that allows companies to respond quickly to changes in demand. Reducing throughput times and optimizing processes make it easier to bring new products to market more quickly and meet customer requests in a timely manner.
Lean principles emphasize the importance of involving all employees in the improvement process. Everyone in the company, regardless of their position, is encouraged to contribute ideas for optimization. This not only promotes a sense of responsibility, but also increases employee motivation and satisfaction. Such a culture of cooperation and appreciation has a positive effect on the entire working atmosphere.
By consistently reducing waste and using resources efficiently, lean principles also contribute to environmental sustainability. Less material consumption, reduced energy costs and optimized logistics reduce a company's ecological footprint. At the same time, continuous improvement and constant adaptability lay the foundation for long-term economic success.
Ultimately, lean production aims to put the customer at the center. By focusing on value-added activities and improving quality, companies can offer products and services that not only meet, but often exceed, customer expectations. This leads to higher customer satisfaction, which is directly reflected in a stronger market position and increased competitiveness.
LEAN Production toolbox
- Value Stream Mapping
- 5S method
- Material supply
- Kaizen (continuous improvement)
- Shop floor management
- Assembly optimization
- SMED
Value Stream Mapping
Value stream analysis is a fundamental tool in the lean approach. It makes it possible to visualize the entire production process from start to finish and to identify weak points and non-value-adding activities. Through this analysis, companies can identify bottlenecks, shorten lead times and reduce waste. Click here for our value stream design training
5S method
The 5S method aims to organize and standardize the workplace. It includes the steps of sorting, systematizing, cleaning, standardizing and self-discipline. This method creates a clean, tidy workspace that increases productivity and increases safety. Click here for our 5S training
Material supply
Kanban is a visual control system that regulates the flow of materials in production. It relies on visual signals such as maps or boards to signal the need for materials. This helps reduce overproduction and inventory levels while minimizing shortages and disruptions.
Kaizen (continuous improvement)
Kaizen is the principle of continuous improvement. It encourages employees to constantly look for and implement process optimization opportunities. Through small, incremental changes, companies can continually increase their efficiency.
Shop floor management
Shop floor management is a crucial approach to increasing efficiency in manufacturing. It refers to the direct monitoring and control of production processes at the factory level. Through clear communication, regular meetings and visual management methods, bottlenecks, problems and potential for improvement are identified. This enables rapid response to optimize production processes and minimize waste. Shop floor management also promotes the involvement of employees in the continuous improvement process, which leads to increased motivation and effectiveness. Ultimately, this approach strengthens the competitiveness of companies in a dynamic market environment.
Assembly optimization
Optimize production processes, shorten throughput times and reduce costs. This strategy aims to make assembly processes more efficient and smoother, ultimately increasing overall production output. Assembly is a critical step in manufacturing that has a significant impact on production costs, quality and delivery times. Optimizing this process helps minimize bottlenecks, reduce production times and increase efficiency, ultimately leading to higher customer satisfaction and competitiveness.
SMED
SMED (Single-Minute Exchange of Die) is a method for reducing setup times reducing them to single-digit minutes Internal and external setup processes are separated to enable parallel processes. Flexibility and efficiency with quick-clamping systems and optimized processes . SMED makes production processes leaner and more economical – a win for every company. Click here for our SMED training/workshop