Factory planning
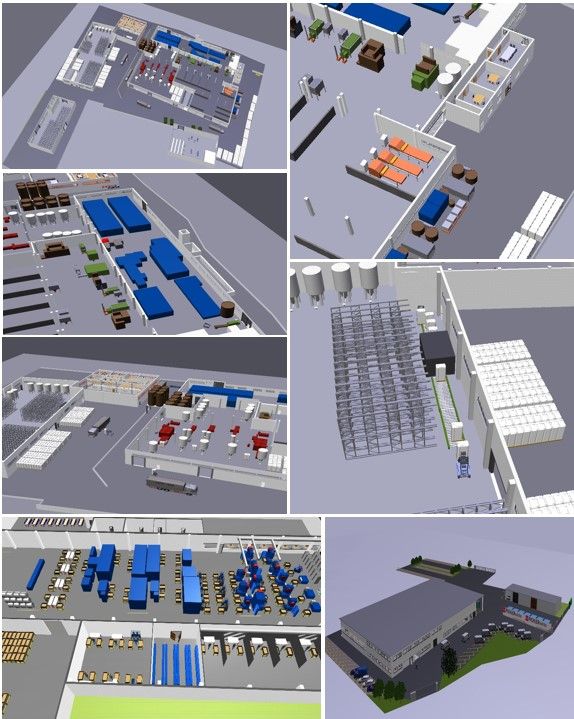
The planning, optimization and implementation of production and logistics locations, whether on greenfield sites or in existing buildings, is one of the most challenging tasks for companies.
Mistakes made in the planning and implementation phase are very difficult or impossible to correct later. We support companies from finding a location to the complete realization of works.
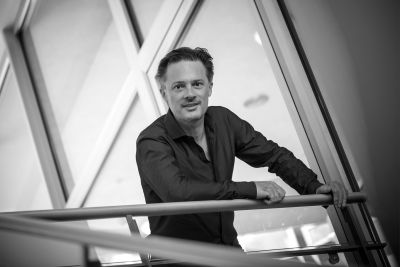
Walter Meitz
Your contact for all questions, references, process, etc.
Walter Meitz
+43 664 654 06 79
This email address is stez protected from spambots. You need javaScript Enabled to view it.
Range of services
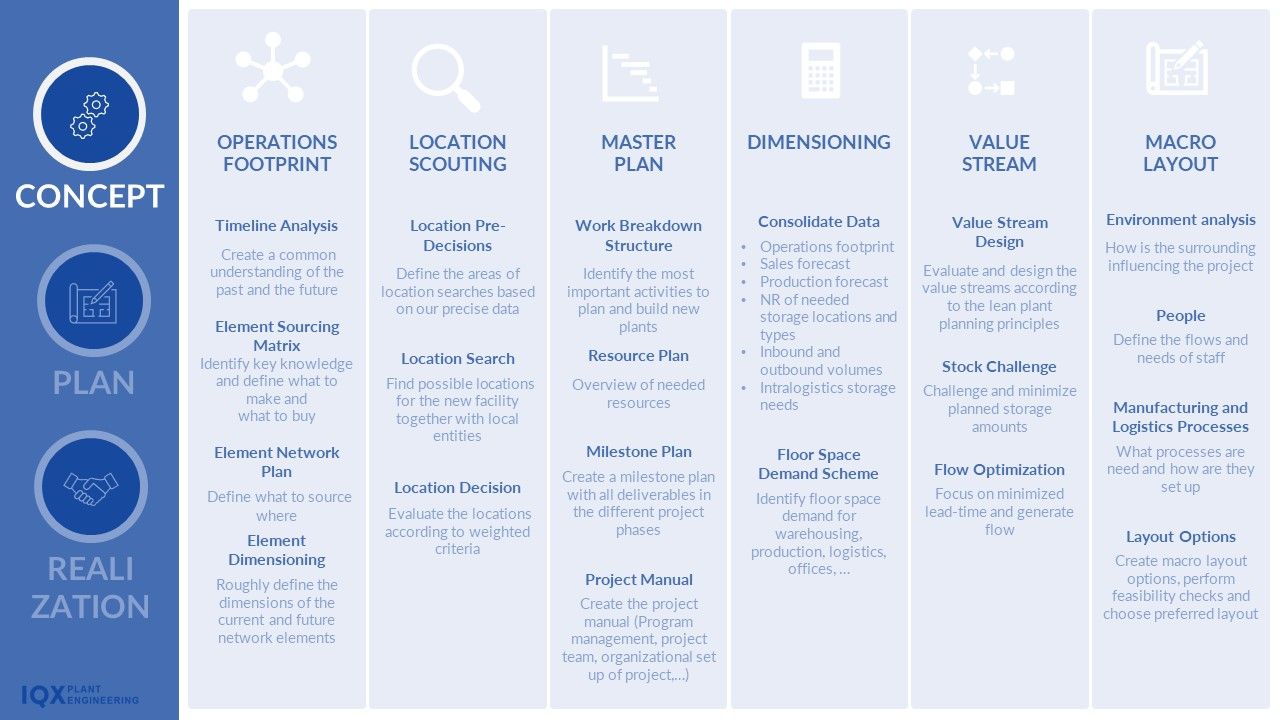
The term “operations footprint” refers to the entirety of a company’s operational locations and activities. This is not just about the geographical distribution of production sites, warehouses and distribution centers, but also about the strategic alignment of the entire value chain. An optimized operations footprint ensures that operational processes are designed efficiently, cost-consciously and sustainably to best support the company's goals.
The method for analyzing and optimizing the operations footprint begins with a comprehensive inventory. All locations and their functions are recorded and evaluated in detail. It's about understanding how each location contributes to the overall success of the company and what costs are associated with it. External factors such as market requirements, supply chain risks and geopolitical influences are also taken into account.
The next step is a strategic assessment. The aim is to find out whether the current structure meets future requirements. For this purpose, various scenarios are developed that simulate different market and cost developments. These scenarios help to highlight opportunities and risks and provide valuable information about where a realignment might be necessary.
The implementation of the optimization measures then requires careful planning and close coordination between the departments involved. It's about harmonizing processes, using synergies and possibly repositioning or even consolidating locations. It is important that the transition takes place smoothly and that continuity in operational business is guaranteed.
An optimized operations footprint can not only reduce costs, but also increase the company's flexibility and responsiveness. In an ever-changing global economy, this is increasingly becoming a key competitive advantage. Our goal is to work with you to create a future-proof structure that enables growth while meeting the requirements of today and tomorrow.
**Location scouting for a new factory location** is a crucial process in a company's strategic planning. This involves the systematic search and evaluation of potential locations that optimally meet the specific requirements of the planned factory. The aim is to find a location that offers the greatest possible benefit from an economic perspective as well as in terms of logistical, ecological and social factors.
### Procedure for location scouting
1. **Definition of location criteria:**
The first step in location scouting is to define clear criteria that the new location must meet. These criteria can be diverse and include:
- **Cost factors:** Property prices, taxes, subsidies, energy costs and wage levels.
- **Logistical aspects:** Proximity to suppliers, customers, transport connections (roads, railways, ports, airports) and infrastructure.
- **Labor market:** Availability of qualified workers, training opportunities and labor market regulations.
- **Environmental factors:** Environmental regulations, climate conditions, energy sources and sustainability potential.
- **Social and cultural factors:** Quality of life for employees, cultural fit and social acceptance.
2. **Location data collection and analysis:**
Once the criteria are set, data collection on potential locations begins. This includes the analysis of macro and micro factors:
- **Macro factors:** Economic stability, political environment, trade agreements and legal aspects.
- **Microfactors:** Availability of infrastructure, specific location costs, market potential and regional characteristics.
3. **Evaluation of potential locations:**
The locations are evaluated and compared with each other based on the data collected. Scoring models are often used here, in which each location receives points according to the defined criteria. The locations with the highest overall points are then considered for closer consideration.
4. **On-site visits and detailed analyses:**
The most promising locations are then visited on site. Specific circumstances are examined, such as the nature of the terrain, proximity to supply networks and actual accessibility. Discussions are often held with local authorities and potential partners to clarify legal and organizational questions.
5. **Risk Analysis and Decision Making:**
A comprehensive risk analysis is carried out before the final decision is made. Possible risks such as political instability, natural disasters, supply chain risks or social conflicts are assessed. Based on this analysis, the company then makes the decision for the optimal location.
6. **Negotiations and conclusion of contract:**
After the site selection, negotiations follow with the property owners, local authorities and other relevant actors. It's about securing the best conditions for the company, including legal and tax frameworks, investment incentives and other advantages.
7. **Planning the implementation:**
Once the location is determined, detailed planning of the factory begins. This includes architectural design, logistics planning, compliance with environmental regulations and the integration of the site into the existing production and supply chain.
A Work Breakdown Structure (WBS) is a project management tool that divides a project into smaller, manageable units. It is used to represent all the work required to achieve a project goal in a hierarchical structure. The overall project is broken down into larger components, which in turn are broken down into detailed work packages. These packages are the smallest units that can be planned and managed, allowing clear assignment of tasks and responsibilities. The WBS offers a clear overview, facilitates planning and control, and improves communication within the project team.
Resource planning involves determining and allocating the necessary resources such as personnel, materials, time and budget to successfully complete a project. It ensures that the required resources are available in the right quantities, at the right time and in the right place. This also includes taking capacities, availability and costs into account to ensure efficient use and avoid bottlenecks or overloads.
A milestone plan is an overview of the important stages of a project, defined as key progress points. It is used to monitor project progress by marking fixed points in time at which certain results or subgoals must be achieved. As a result, the milestone plan provides clear orientation and helps to control the course of the project and react to deviations in a timely manner.
A project manual is a comprehensive document that brings together all the essential information and guidelines for planning, implementing and controlling a project. It serves as a central reference for the entire project team and ensures that everyone involved is informed about the goals, roles and responsibilities, schedules, resources, communication channels and decision-making processes. By clearly documenting procedures, standards and processes, the project manual ensures a uniform way of working and helps to avoid misunderstandings and inefficiencies during project implementation. It is a living document that will be updated as the project progresses to reflect changes and new insights.
A **Shopfloor Demand Scheme** is a strategic system used in the manufacturing industry to precisely control and synchronize material and production requirements directly on the factory floor, the so-called shop floor. The aim of this scheme is to optimally adapt material supply and production processes to actual needs in order to achieve high efficiency, minimal inventory and short lead times.
At the core of the Shop Floor Demand Scheme is the idea that materials and parts are made available exactly when they are needed in production - no sooner and no later. This is often achieved through the use of just-in-time (JIT) principles or Kanban systems, which ensure that production is continuously supplied with the required materials without building up unnecessary inventory.
The system works by recording the actual requirements that arise directly on the shop floor and immediately converting them into production orders or material requirements. This happens in real time, so that production can react flexibly and quickly to changes in demand. For example, if a particular production line requires a higher quantity of a particular part, this is immediately noted in the system and the material flow is adjusted accordingly to meet this demand.
Another advantage of a shop floor demand scheme is the improvement of transparency and communication on the factory floor. Because the system accurately and promptly maps demand, production managers and employees can immediately see what materials and resources are needed and when they need to be provided. This reduces the need for manual intervention and planning adjustments, which in turn reduces error rates and increases efficiency.
Overall, a Shop Floor Demand Scheme supports smooth and continuous production that is closely synchronized with actual demand. It helps reduce costs, increase production flexibility and shorten delivery times by ensuring that all the materials and parts needed are available exactly when they are needed. This makes it an essential tool in modern manufacturing, especially in environments where high efficiency and rapid responsiveness to market changes are critical.
**Value Stream Design** (or **Value Stream Mapping**) is a method in lean management that is used to analyze and optimize the entire processes within a value chain. The goal is to identify waste, increase efficiency and maximize value for the customer.
Value stream design looks at all the steps necessary to bring a product or service from raw materials or orders to the finished product to the customer. It includes not only the physical processes of production, but also the information flows that control these processes. By visualizing the entire value stream in detail, inefficient processes, bottlenecks, overproduction, and other types of waste can be uncovered.
Value stream design process
1. Preparation and goal definition
At the beginning, the target state is defined, i.e. what is to be achieved with the value stream analysis. It is determined which products or services are to be analyzed and who is involved in the analysis.
2. Recording the current state
In the first step, the current value stream is recorded and visualized. The entire process, from receipt of raw materials or information to delivery of the finished product, is presented in detail. Both the physical processes (such as material flow and production steps) and the information flows (such as orders and control processes) are mapped.
3. Current state analysis
After the current state is captured, it is analyzed to identify non-value-adding activities. The goal is to make bottlenecks, delays, unnecessary movements, overproduction, waiting times and other waste visible.
4. Development of the target state
Based on the analysis, an optimized target state is developed. Processes are redesigned or eliminated to make the value stream more efficient. The focus is on maximizing value creation and minimizing waste. Lean principles such as just-in-time, Kanban or pull systems are often introduced.
5. Implementation planning
After the target state has been defined, a detailed implementation plan is created. This plan determines which measures should be implemented in which order, who is responsible for them and what resources are needed.
6. Implementation and monitoring
The new value stream is implemented and the changes are put into practice. During implementation, it is important to continuously monitor progress and ensure that the planned improvements actually achieve the desired effects.
7. Continuous Improvement
Value stream design is an iterative process. After implementing the new value stream, the process is regularly reviewed to identify further opportunities for improvement. The cycle of capture, analysis and improvement continues to continuously optimize value creation.
A **rough layout** of a new factory is created as part of factory planning in order to obtain an initial, comprehensive overview of the spatial arrangement of the most important areas and processes within the factory. It serves as a fundamental planning tool to ensure that the basic requirements for material flow, production processes, logistics and infrastructure are optimally taken into account.
The rough layout allows potential problems and bottlenecks to be identified early on, which could later lead to inefficient processes or additional costs. It helps to place the locations of production lines, warehouses, administrative areas and other important facilities so that the entire production process runs as efficiently as possible.
The rough layout is a crucial planning tool that makes it possible to compare alternative layouts, select the best options and create a solid foundation for the detailed elaboration of the final factory layout. It helps to minimize risk and ensures that all key planning aspects are taken into account at an early stage before moving on to detailed planning and construction.
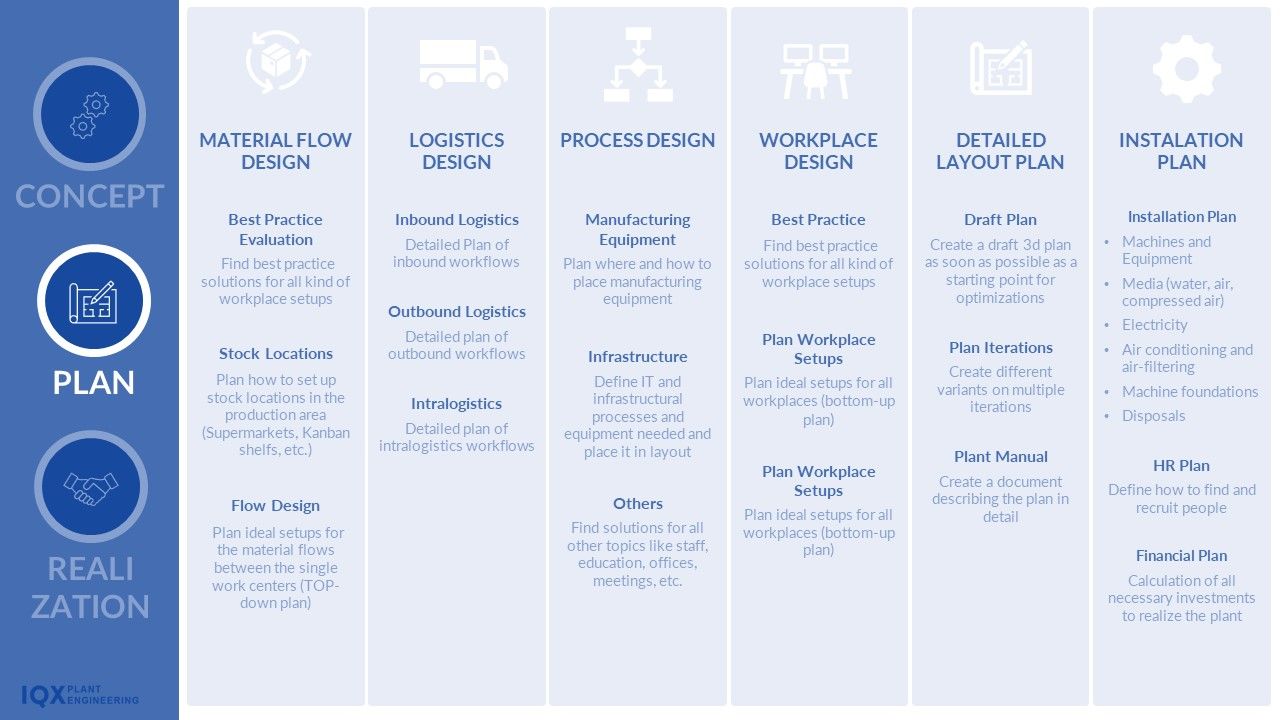
Material flow design as part of factory planning refers to the systematic design and optimization of the flow of raw materials, semi-finished products and finished products within a factory. The aim is to design the flow of materials so that production processes run efficiently, cost-effectively and smoothly, while at the same time minimizing unnecessary movements, waiting times and inventory levels.
In detail, material flow design includes the planning of the routes and means of transport that lead materials through the various production stages. It takes into account the placement of machines, storage areas, assembly bays and shipping areas to ensure that materials are transported through the factory in the shortest and most efficient route. The use of conveyor technology, automated transport systems and storage technologies is also taken into account.
A well-thought-out material flow design contributes significantly to the productivity and competitiveness of a factory as it helps to shorten production times, reduce costs and increase the flexibility of manufacturing processes. It ensures that all logistics within the factory are optimally aligned with production requirements, ultimately leading to more efficient and leaner production.
**Logistics design** as part of factory planning refers to the strategic design and optimization of the entire logistical processes inside and outside the factory. It includes the planning and coordination of all activities associated with the transportation, storage, handling and distribution of materials, components and finished products.
Logistics design aims to make the flow of goods and information as efficient as possible in order to minimize costs, shorten delivery times and ensure the availability of the required materials. It takes into account various aspects such as the location of warehouses, the design of storage systems, the selection and implementation of transportation and handling technologies, and the integration of supply chain management.
An effective logistics design ensures that all logistical processes mesh seamlessly and are optimally coordinated with the production processes. This helps to avoid bottlenecks, increase flexibility and ultimately make the entire value chain more efficient and competitive. It includes both internal logistics (e.g. the flow of materials within the factory) and external logistics (e.g. the procurement of raw materials and the distribution of finished products).
**Process design** in the context of factory planning refers to the development and optimization of the production processes that occur within the factory. It includes the detailed planning of all work steps that are necessary to transform raw materials into finished products. The goal of process design is to create efficient, cost-effective and high-quality production processes that meet the needs of the company and the market.
Various aspects are taken into account as part of the process design:
- **Process planning**: This determines the order in which the individual production steps take place and how they are linked to each other to ensure a smooth and efficient production flow.
- **Technology selection**: It is decided which machines, systems and technologies will be used to carry out the production steps. The selection of the optimal technology plays a central role in optimizing quality, speed and costs.
- **Workplace design**: The layout and equipment of workstations is planned to maximize employee productivity while meeting ergonomic and safety requirements.
- **Quality Control**: Measures and controls are integrated to ensure the quality of products at every stage of the production process.
Process design is closely linked to material flow design and logistics design as it ensures that the production processes are efficiently integrated into the material and logistics structures. A well-thought-out process design minimizes waste, reduces throughput times and helps reduce costs by designing processes so that they are optimally tailored to existing resources and logistical conditions.
Overall, process design forms the backbone of factory planning as it lays the foundation for the effective and efficient manufacturing of products and significantly influences the overall performance of the factory.
Workplace design in factory planning refers to the design and arrangement of workstations to maximize efficiency, safety and ergonomics for employees. It is an integral part of the overall process as it represents the interface between the production processes, the technologies used and the people who work in the factory.
The goal of workplace design is to design workplaces so that employees can carry out their tasks effectively and without unnecessary stress or danger. These include the following considerations:
- Ergonomics: Ensuring that workplaces are designed to be physically comfortable and health-promoting for employees to prevent injuries and fatigue. This includes proper height of work surfaces, convenient access to tools and materials, and minimization of repetitive, stressful movements.
- Efficiency: Workplaces are designed so that materials, tools and machines are optimally arranged to avoid unnecessary paths and movements. This promotes greater productivity and reduces the time it takes to complete a task.
- Safety: Integrating safety measures into workplace design to minimize the risk of accidents and injuries. This can be achieved through the placement of guards, clear safety instructions and consideration of escape routes.
- Flexibility: Workstations can be designed to be adaptable to different tasks and production requirements. This is particularly important in modern factories that need to respond quickly to changes in production.
Workplace design is closely related to process design as it represents the physical implementation of the planned production processes. A well-designed workplace allows employees to make production processes more efficient, which in turn leads to higher overall productivity and quality. Combined with material flow and logistics design, workplace design helps the entire factory function optimally, maximizing both employee performance and well-being.
In the detailed planning phase of factory planning, the previously developed concepts and layouts are concretized and implemented into detailed plans. The aim of this phase is to plan all aspects of the factory down to the smallest detail to ensure that construction and commissioning go smoothly and that the factory functions optimally.
Essential steps in the detailed planning phase
1. Factory layout detailing:
The rough layout developed in earlier phases is converted into a detailed layout. All production areas, storage areas, traffic routes, supply lines and workplaces are precisely planned and recorded in the final plans.
2. Integration of 3D planning:
In the detailed planning phase, **3D planning** is increasingly being used to enable an even more accurate and realistic representation of the factory. All areas of the factory can be modeled virtually using 3D software. This enables comprehensive visualization of the layout of machines, systems and workstations, making it easier to identify potential problems or bottlenecks. The 3D models also offer the opportunity to understand and optimize complex relationships between the various systems and structures at an early stage.
3. Planning the technical infrastructure:
All technical systems, such as energy supply, water and wastewater systems, ventilation and air conditioning, as well as IT and communication networks, are planned in detail. The integration of these systems into the 3D model is also taken into account to ensure that all cables and connections are laid correctly and that there are no collisions with other components.
4. Specification of machines and systems:
In this phase, the exact specifications of the machines and systems are determined. This includes selecting equipment, determining exact installation locations, planning interfaces to other systems and considering maintenance requirements. 3D planning helps to place the machines precisely in the layout and to ensure their accessibility and operability.
5. Workplace design and ergonomics:
The detailed design of the workstations is carried out taking into account ergonomic principles in order to maximize the efficiency and safety of employees. With 3D planning, workstations can be tested virtually to ensure that they are optimally designed ergonomically and that all tools and materials are easily accessible.
6. Simulation and optimization:
Another application of 3D planning in the detailed planning phase is the simulation of material flows, production processes and movement sequences. These simulations make it possible to check the efficiency of the planned processes and to identify and eliminate possible bottlenecks or inefficiencies before the factory is built.
7. Preparation of the construction work:
The construction work is prepared based on the detailed plans. This includes the creation of construction plans, coordination with construction companies and suppliers, as well as planning the construction process. The 3D models also serve as a means of communication between planners, engineers and construction companies to ensure that everyone involved has a uniform vision of the project.
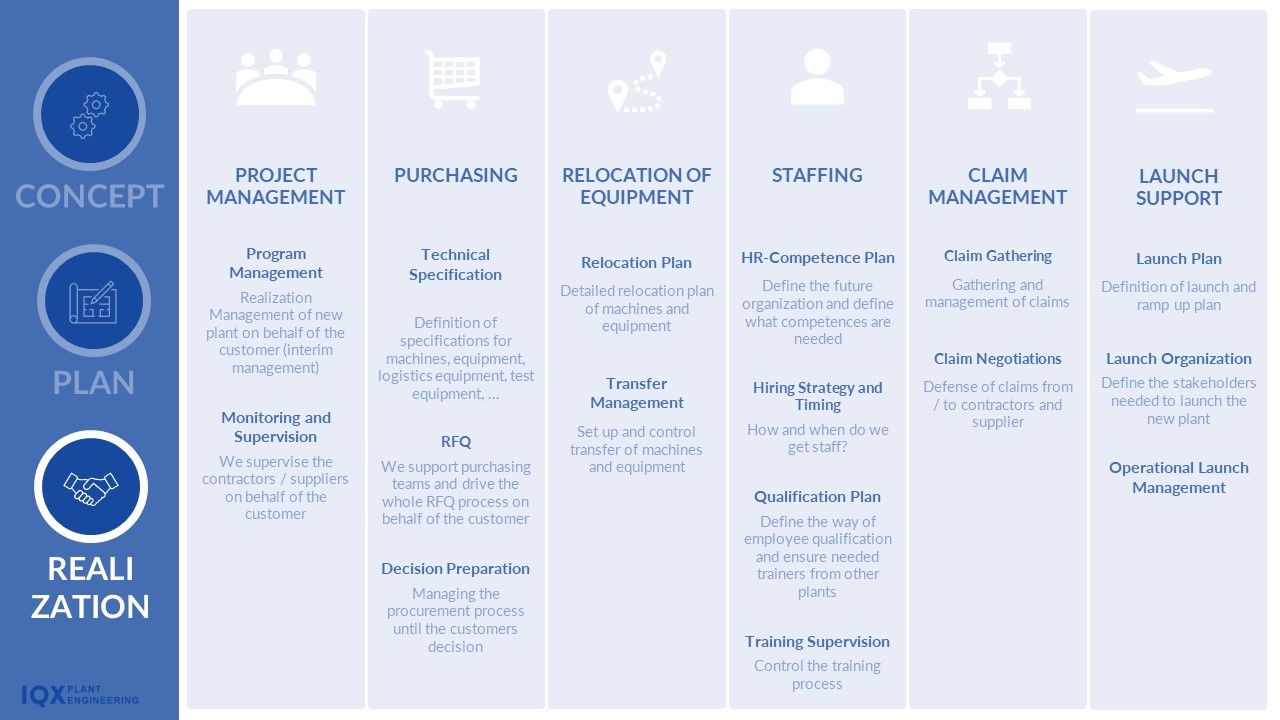
During implementation as part of construction project management, the plan developed in the detailed planning phase is put into practice. This process includes several key activities that ensure that the construction of the factory is completed efficiently, on time and within budget.
Essential steps in construction project management
1. Mobilization and preparation:
First, the construction site is set up and all necessary resources, such as materials, machines and workers, are made available. It is ensured that all permits are in place and that the construction site complies with safety regulations.
2. Monitoring and controlling construction work:
During construction work, construction project management continuously monitors the progress. This includes coordinating the various trades, ensuring compliance with the construction schedule and checking the quality of the work carried out. Regular construction site meetings with everyone involved ensure that everyone is on the same page and any problems can be solved quickly.
3. Cost and schedule management:
A central aspect of construction project management is monitoring costs and schedules. It is ensured that the construction stays within the set budget and that the planned milestones and completion dates are met. This includes managing change orders and adjusting the plan if unforeseen events occur.
4. Quality control and acceptance:
Regular quality controls are carried out to ensure that the construction work meets the required standards. This includes both checking the construction work and compliance with the technical specifications. At the end of each construction phase, an inspection is carried out to check whether all work has been completed properly.
When purchasing machinery, systems and technical equipment for a new factory, there are several important aspects to consider to ensure that the purchases meet the requirements of production and are economical and efficient in the long term.
1. Requirements analysis
Before purchasing, a precise analysis of the requirements is necessary. This includes defining the technical specifications that the machines and systems must meet in order to achieve the production goals. Aspects such as performance, capacity, flexibility and compatibility with existing systems should be taken into account.
2. Quality and reliability
The quality of the machines and systems is crucial for smooth operation. It is important to pay attention to the reliability and longevity of products to minimize downtime and maintenance costs. The choice should therefore fall on proven manufacturers and technologies that are known for their reliability.
3. Costs and Budget
In addition to the initial costs, long-term operating costs must also be taken into account, including maintenance, energy consumption and spare parts. A comprehensive cost-benefit analysis helps identify the most economical option. The possibility of financing or leasing should also be examined in order to optimize the investment.
4. Delivery times and availability
The delivery times of the machines and systems must be coordinated with the factory's construction schedule. Delays in delivery can jeopardize the entire project plan. It is therefore important to clarify delivery times and, if necessary, examine alternatives in order to avoid bottlenecks.
5. Service and support
Reliable after-sales service is crucial for the long-term operational reliability of the machines. This includes the availability of technical support, rapid supply of spare parts and the possibility of regular maintenance. It is advisable to carefully examine the service offerings from manufacturers and ensure that they meet the requirements.
6. Technological compatibility
The new machines and systems must be able to be seamlessly integrated into the existing or planned production environment. This includes compatibility with other technical systems, automation solutions and IT infrastructures. A lack of integration can lead to significant losses in efficiency.
7. Certifications and regulations
It must be ensured that the machines and systems comply with all relevant legal regulations and industry standards. This primarily concerns safety standards, environmental regulations and energy efficiency guidelines. Compliance with these regulations is not only important for legal reasons, but also contributes to the sustainability of the operation.
8. Training and usability
The operation of the new machines should be as intuitive and simple as possible in order to minimize the training time for personnel. The supplier should provide education and training to ensure staff can operate the machines safely and efficiently.
9. Future security
When selecting machines, future security should also be taken into account. This includes the possibility of adapting or expanding the machines to future requirements. Investing in flexible and scalable technologies can help prepare the factory for future changes.
10. Contract design
The contractual conditions for the purchase of machines and systems must be carefully negotiated. Important points are warranty conditions, liability, payment methods and delivery conditions. It is advisable to seek legal advice to ensure that all important aspects are covered contractually.
Purchasing machines, systems and technical equipment is a complex process that requires careful planning and analysis. By taking the aforementioned aspects into account, it can be ensured that the investments made optimally support production and are economical and efficient in the long term.
**Relocation management** when building a new factory is a comprehensive and complex process that goes far beyond the mere physical relocation of machinery and equipment. The aim is to transfer the entire production capacity from an existing location to a new one without significantly disrupting ongoing operations and thereby maintaining or even increasing production efficiency.
The first step in relocation management is detailed planning. Schedules are developed that cover the entire process from dismantling the machines to putting them back into operation at the new location. It is critical that these schedules are realistic and include enough buffer for unforeseen events to avoid production downtime. The coordination of the various activities – from logistics to new installations to employee training – must be recorded in a precise schedule.
Another important aspect is resource coordination. This includes ensuring that all required materials, machines and equipment are available at the new location on time and are installed properly. This requires close collaboration with suppliers, transport service providers and internal teams. The physical relocation of the machines is particularly critical as they are often sensitive and expensive. Therefore, the transport, securing and reconstruction of these systems must be carefully planned and carried out to avoid damage.
Employee engagement plays a central role in relocation management. Employees must be involved in the relocation process and trained to use the machines and processes at the new location. This is particularly important when new technologies or changing workflows are introduced. Training should be carried out early and comprehensively to ensure that staff can continue to work seamlessly in the new location.
The test runs at the new location are another critical phase of relocation management. Before final commissioning, all machines and systems must be thoroughly tested to ensure that they function properly and that production can begin as planned. These test runs are also used to make final adjustments and ensure that material flow and workflows are optimized.
Risk management is paramount throughout the entire relocation process. It is important to identify potential risks such as production interruptions, delays, transport damage or problems with restarting at an early stage and to plan appropriate countermeasures. These include, for example, emergency plans, alternative supply chains or additional resources that can be quickly mobilized in the event of complications.
Overall, relocation management is a strategic process that requires careful planning, close coordination and precise execution. Successful implementation ensures that production capacities at the new location can be taken over efficiently and without major interruptions. This helps ensure that the factory runs optimally right from the start and that the set goals in terms of productivity and efficiency are achieved.
Staffing, i.e. staffing in a new factory, is about recruiting and integrating the right employees in sufficient numbers and with the right qualifications for the different positions. The process begins with a detailed needs analysis where the required roles and skills are defined. This determines which positions are necessary, which specific skills the employees must have and how many employees are needed in the different areas.
This is followed by the recruitment phase in which suitable candidates are sought. This can be done both internally, by transferring or upskilling existing employees, and externally, by recruiting new talent. The recruitment process must ensure that the selected candidates not only meet the technical requirements, but also fit the company culture.
Once the employees are selected, the induction and training phase begins. It is important here that new or transferred employees are comprehensively prepared for their tasks. This includes training on specific machines and processes, but also instructions on safety guidelines and quality standards. The onboarding phase should be well structured to ease the transition into the new role and ensure productivity from the start.
Throughout this process, it is crucial to ensure open communication and clear expectations. Employees should always know what is expected of them, what development opportunities they have and how their role contributes to achieving company goals. In addition, aspects such as working conditions, remuneration and possible career paths must be discussed early and transparently in order to ensure high employee satisfaction and loyalty.
When it comes to staffing, it is also important to take a long-term perspective. This means not only meeting current needs, but also keeping an eye on potential future needs. Topics such as the training of employees, the creation of young talent and the management of knowledge transfer play an important role here.
In summary, staffing is a complex process that requires careful planning and implementation to ensure that the new factory is staffed with the best available talent and that they are effectively integrated into workflows. Targeted staffing lays the foundation for a smooth start to production and the long-term success of the factory.
Claim management is of central importance not only in the construction process of a factory, but also in the purchasing and installation of machines and systems. In a project of this size, a variety of challenges can arise that lead to deviations from the original contract. These deviations may result in additional costs, delays or technical problems affecting both the construction and commissioning of the factory.
When building a factory, unforeseen events can occur such as delays in the construction process, changes in building regulations or unexpected ground conditions. These may require additional work and costs not included in the original contract. Without effective claims management, such situations could lead to disputes between the owners, contractors and subcontractors, which could jeopardize the entire project.
The situation is similar when purchasing and installing machines and systems. Problems such as delivery delays, deviations from the agreed specifications or difficulties during installation can arise. These can have a significant impact on the project schedule and budget. Claim management ensures that all contractual obligations are met and that appropriate compensation or adjustments can be negotiated in the event of deviations.
Claim management is therefore essential to ensure that both the construction process and the installation and commissioning of technical equipment run smoothly and within budget and schedule. It helps to identify potential conflicts early and resolve them before they escalate, thereby contributing to the successful completion of the project.
Start-up management is crucial to ensure the smooth start of a new factory or production line. This phase is about ensuring that all systems, machines, processes and personnel are optimally prepared for the start of production. An inefficient start-up can lead to significant problems, such as production delays, quality defects or unexpected costs, which can affect the overall success of the factory.
Good start-up management makes it possible to identify potential problems early and resolve them before they disrupt operations. It includes reviewing and fine-tuning production processes, training staff and conducting test runs to ensure production goals are met from the start. Additionally, it plays an important role in promoting communication and coordination between different departments and stakeholders to ensure that everyone is on the same page and working together towards a successful launch.
Effective start-up management minimizes the risks associated with starting new production. It ensures that production can be ramped up quickly, quality remains stable and the company achieves its market launch goals. At a time when speed and efficiency represent key competitive advantages, a smooth start-up is a key factor in the long-term success of a new factory.
Project examples
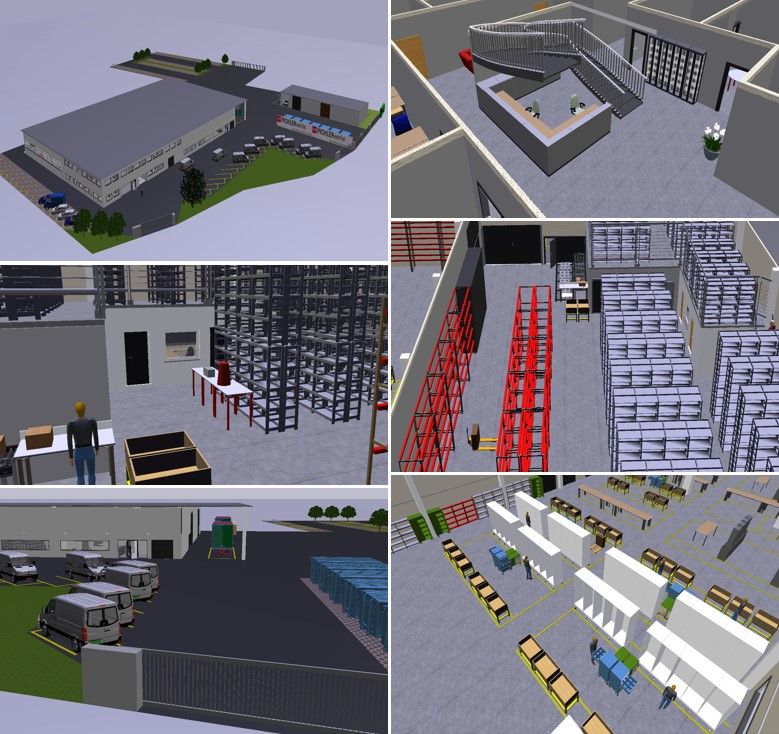
New plant planning for
control cabinet construction
Styria / Austria
Detailed planning of the logistics processes
Detailed planning of the production processes
Office planning
Assembly optimization
Economic considerations
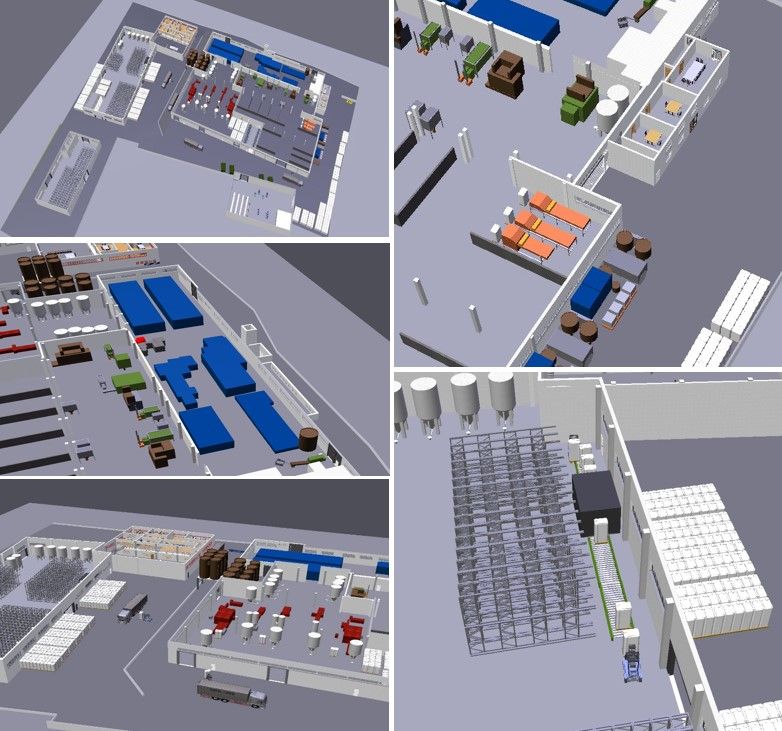
Plant expansion planning
recycling plant
Venice, Italy
Detailed planning of the logistics processes
Detailed planning of the production processes
Office planning
Infrastructure planning
Implementation planning
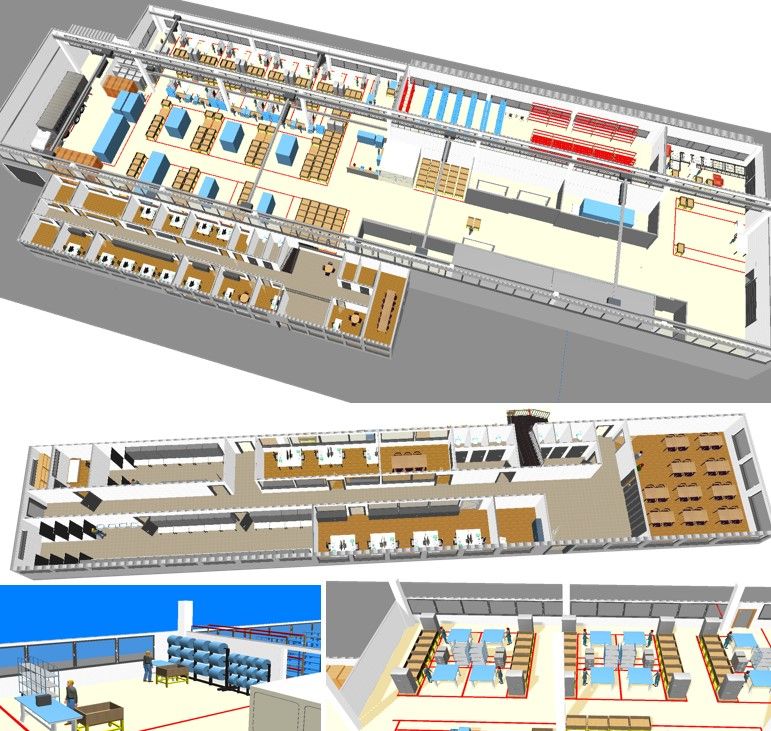
Plant re-planning
assembly plant
Satu Mare / Romania
Warehouse planning
Assembly planning
Production process planning
Office planning
Infrastructure planning
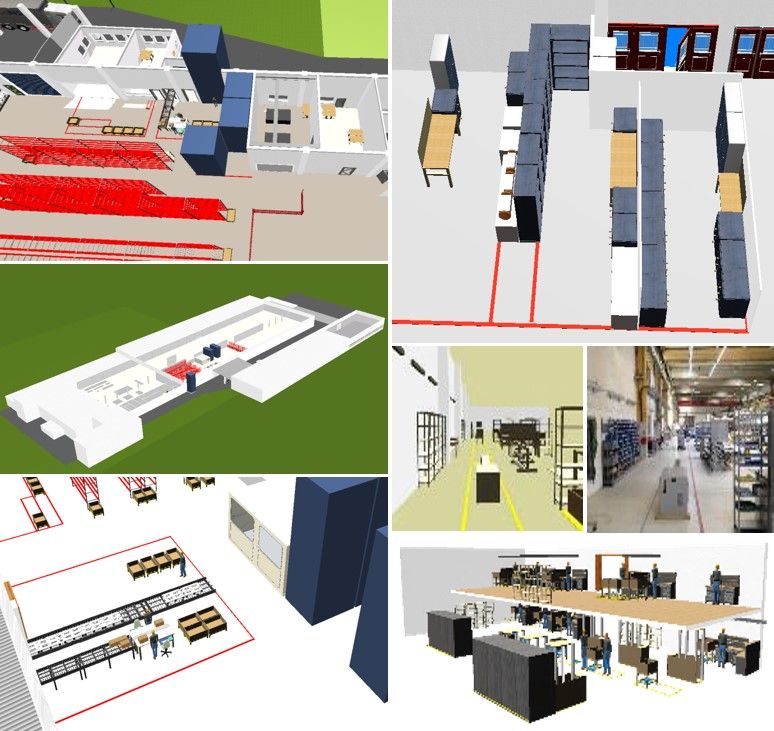
Plant re-planning
assembly plant
Styria / Austria
Analysis of logistics processes
Warehouse concept planning
Assembly planning
Infrastructure planning
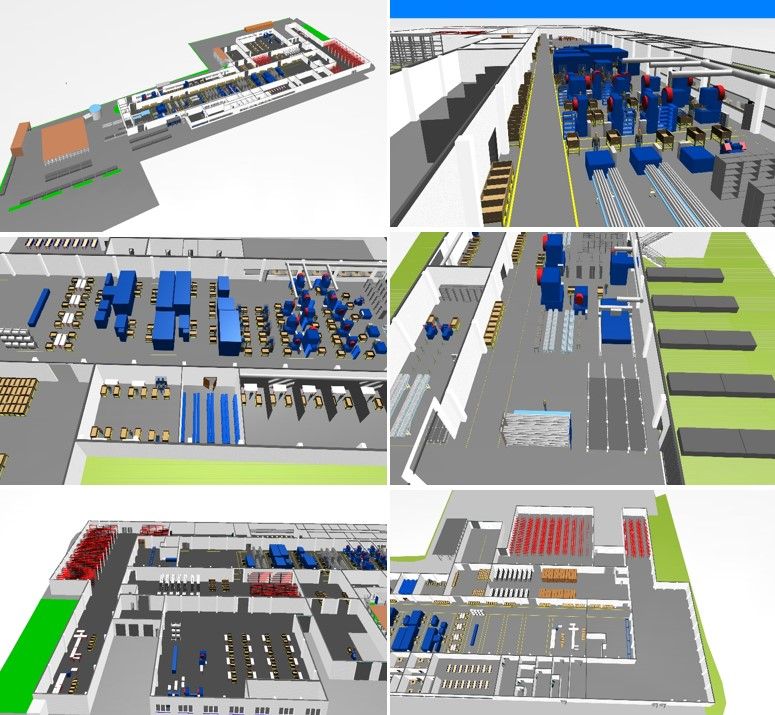
Factory transfer
component factory
Slovakia West
Analysis of the logistics processes
Warehouse concept planning
Brownfield planning
Warehouse planning
Infrastructure planning
Transfer support
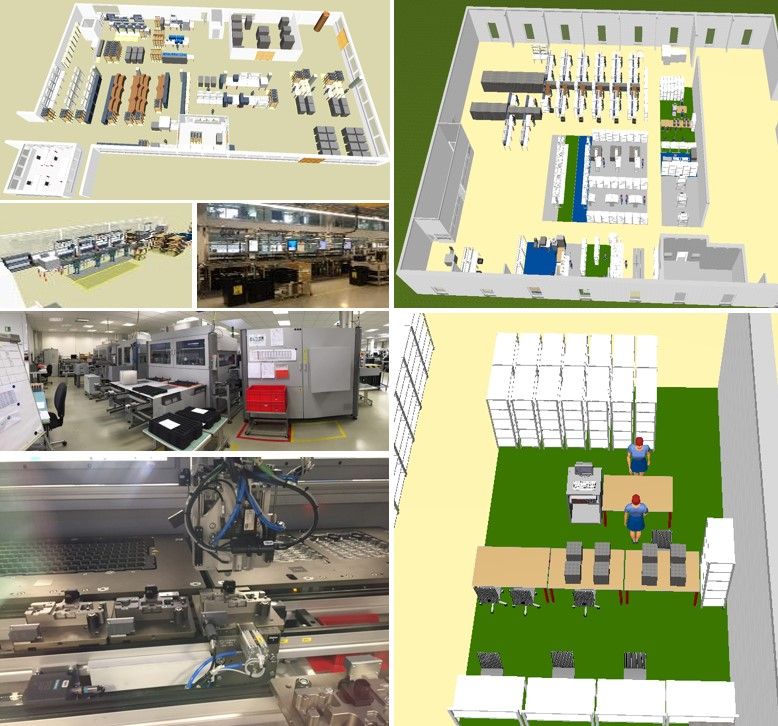
Plant development planning
for the electronics industry
Germany / Hungary
Global Manufacturing Footprint
Detailed planning of all logistics and production processes
Warehouse optimization
Assembly optimization
Project management
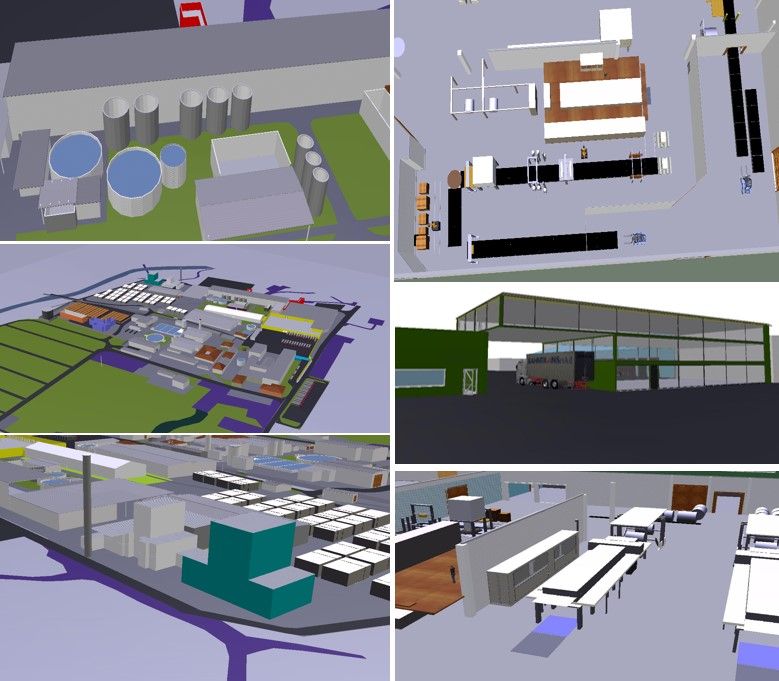